Most Australian mine operators are actively investigating and implementing ways to reduce their carbon footprint or offset their diesel fuel consumption through various carbon neutral initiatives.
Larger companies with the capital means are investing in infrastructure and renewable energy projects such as huge solar farms to reduce their dependence on fossil fuel generated power. Other operations may consider approaching the issue by way of paying carbon offset credits. Some are even converting their haul truck fleet to electric vehicles or are putting significant time and resources into comprehensive forestry rehabilitation programs.
There is certainly no lack of innovative and experimental solutions available to mines wanting to move towards carbon neutrality. However, while these solutions will certainly be effective, they require significant upfront capital investment and the projects can often take many years to complete. This puts a lot of options out of reach for many smaller miners.
The good news is that there are also proven, cost-effective and highly practical transitional strategies available which will achieve a reduction in diesel fuel almost immediately and regardless of the investment in large infrastructure or innovation projects.
The heavy burden of haul trucks on the environment
Haul truck fleets are absolutely essential to the operation of any mine, however these trucks consume huge amounts of diesel fuel by design.
Globally, there are around 28,000 large mine hauling trucks in service today. Almost across the board, these haulers are diesel-powered. Each of these trucks will consume roughly 900,000 litres of diesel per year and make up 30%–50% of their mines’ total energy use.
But with mines relying so heavily on haul trucks, how can fuel usage rates be cut without sacrificing productivity or having to invest in disruptive technologies?
The fundamental link between rolling resistance and diesel fuel consumption
One of the most cost-effective and efficient ways that mines can achieve a reduction in fuel usage is to invest in improving the surface quality of haul roads.
This is because the amount of diesel consumed by haul trucks is dramatically increased when road networks have poor rolling resistance due to rough, uneven and loose surfaces. It is widely accepted in the mining industry that there is a strong correlation between rolling resistance and fuel consumption as illustrated in the chart below.
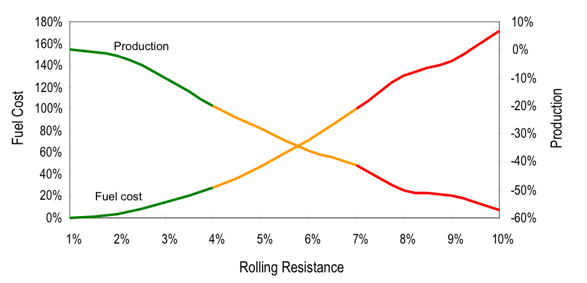
How can mines reduce rolling resistance?
In order to reduce rolling resistance, haul roads need to be carefully designed to ensure they remain smooth, intact and well maintained. A well-constructed haul road should consist of:
- A sub-grade and sub-base layer to ensure that the haul road has sufficient underlying strength to support the weight of the loaded equipment that will be travelling along it.
- Adequate crossfall and super-elevation as well as appropriate drainage
- Development of a surface layer (base course)
- To further improve the running surface, a binder product can be incorporated into the wearing course layer or sometimes even sprayed onto the surface in a series of light delusions.
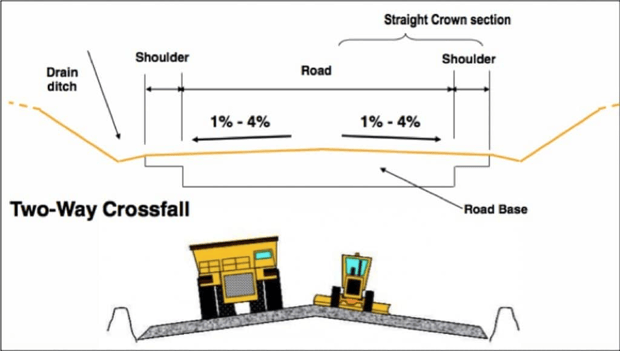
As proven in an independent study conducted by Michelin on behalf of Dust-A-Side, a properly stabilised and sealed road surface can improve rolling resistance by between 20-30% compared with unsealed surfaces.
The test conditions were set to a reduced scale automated truck, at constant speed, with a pulling effort simulating a constant slope of 10% and on stabilised operating conditions.
When comparing a stone-covered (untreated) reference road and a Dust-A-Side treated road, a substantial reduction in fuel consumption of 7.5% could be measured.
Taking into account different trucks and variable speeds and slopes led Michelin to a reasonable conclusion that the overall reduction in hourly fuel consumption was 3%-5% on average on a Dust-A-Side treated haul road. This forward-thinking approach to constructing haul roads leads to smoother roads and much better fuel efficiencies. Ultimately, this means less carbon emissions being released into the atmosphere.
With immediate payback, investing in the treatment of existing haul roads to improve rolling resistance, is a timely and cost effective way for mines of all sizes to reduce diesel fuel consumption rates, alongside the longer term payoff to investing in more disruptive and capitally intensive technologies.